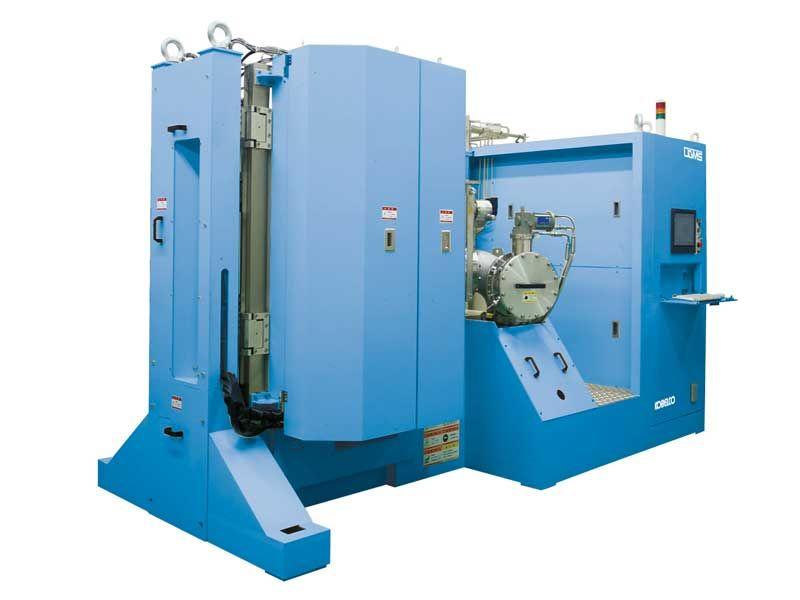
UBMS® SERIES FOR DLC
UnBalanced Magnetron Sputtering
UBMS® series is batch system using Unbalanced Magnetron Sputtering method. Since this system can provide fine and high density films, it is suitable for lubrication film coating such as DLC and Molybdenum disulfide.
- Plasma density is increased near substrate by imbalanced magnetic field.
- Maximization of ion-assist effect.
- Control of Film Properties: Composition, Adhesion, Crystallization, Surface condition.
Argon ion is activated in plasma and hits target. | > | Activated argon ion sputters out metal atom from target. | > | Film deposition is made with sputtered metal ion. |
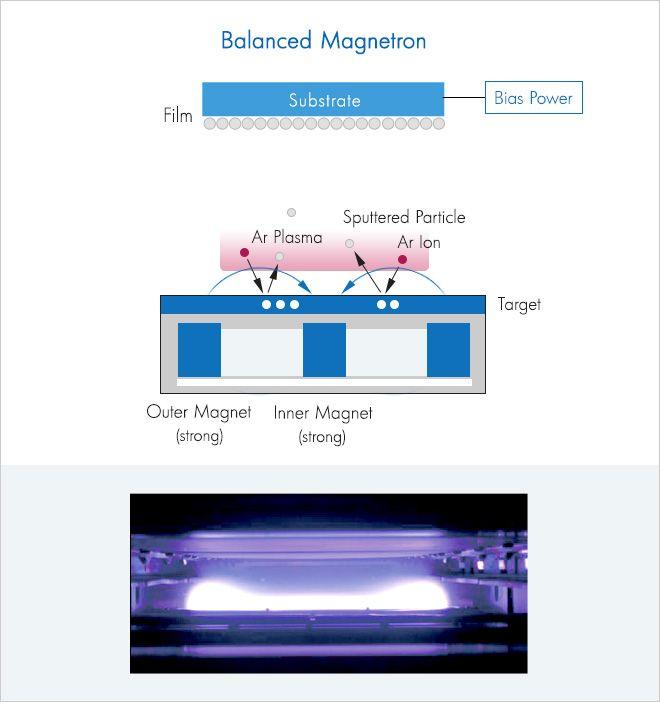
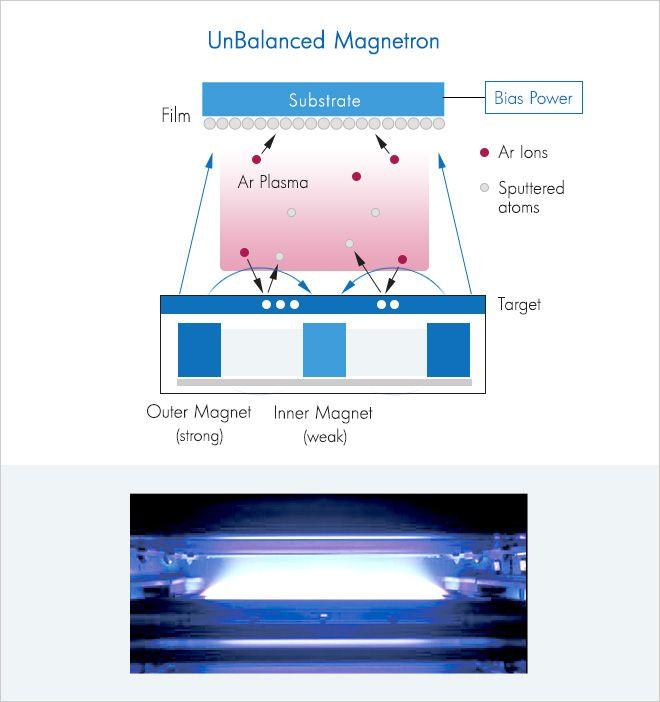

KOBELCO DLC Coating is excellent in wear resistance, low friction and toughness with Nano-multilayered structure.
Well Balanced DLC Film
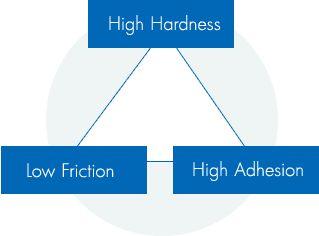
Machine Lineup
![]() |
![]() |
![]() |
Production scale | medium scale production | large scale production |
---|---|---|
Recommended Loading Space |
φ 450mm x H 400mm or φ 130mm x H 400mm x 6 spindles |
φ 700mm x H 800mm or φ 130mm x H 800mm x 12 spindles |
Sputtering Source | 4 | 7 |
Substrate Table | 6-Spindles planetary rotary table | 12-Spindles planetary rotary table |
Features of DLC by UBMS®
DLC (Diamond-like carbon) has widespread applications such as car parts, mechanical components, dies, molds etc. because of its high mechanical hardness, chemical inertness, and low friction behavior. KOBELCO can offer optimized DLC for each customer’s target by tuning coating parameters.
Applications of DLC and more
- Automobile parts (engine parts/ fuel pump parts)
- Mechanical parts (Ball bearing, ball screw, hydraulic pump parts)
- Cutting tools for aluminum
- Spinning tools for aluminum can
- Trimming dies for SUS/Copper tube
- Punches for SUS/aluminum sheet
and more
Advanced DLC by UBMS®
- High Adhesion DLC
- Ion assist effect by UBM
- Optimized Interlayer
- Hardness control and Multi-layer DLC
- Ion assist effect by UBM
- Metal-doped DLC
- Co-sputter with metal target and carbon
- Hydrogen content controlled DLC
- Solid carbon source
- Hybrid coating with AIP
and more
Effect of KOBELCO DLC
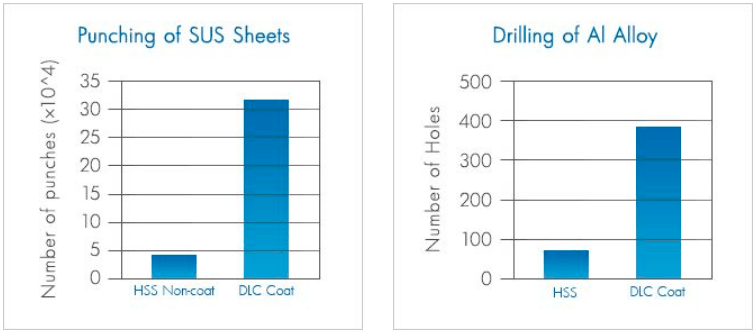
BELCOATTM by UBMS®
Name | Type | Hardness (Hv) |
Thickness (μm) |
Feature & Typical Applications |
---|---|---|---|---|
BELCOAT B |
Standard | 1,500 to 2,500 |
0.5 to 5 |
Balance of Wear Resistance, Lubricity and Adhesion.Common Mechanical Component. |
BELCOAT HB |
High Hardness |
2,500 to 3,500 |
0.1 to 0.2 |
Focused on Wear Resistance Automotive Component Stamping Mold (For Non-Iron, Stainless Steel) |
BELCOAT UB |
Ultra High Hardness |
3,500 to 4,000 |
0.1 to 0.2 |
Focused on Wear Resistance Under High Pressure Automotive Component For Racing Use Cutting Tool(Non-Iron) |
BELCOAT NB |
Nano-Multi Layer |
1,500 to 2,500 |
0.1 to 0.15 |
Balance of Wear Resistance and Lubricity Toughness with Shock Resistant, Bearing, Punching Die |
BELCOAT MB |
Metal Doped | 1,000 to 2,000 |
0.15 to 0.25 |
Property Change by Metal Doping Relief of Film Stress Automotive Component, Plastic Injection Mold |